BIPV, Building Integrated with Photovoltaic, represents an innovative approach to integrating renewable energy technology into building design, offering both environmental and economic benefits. Dorian has taken the first step into this new era and can provide customers with a complete set of BIPV solutions.
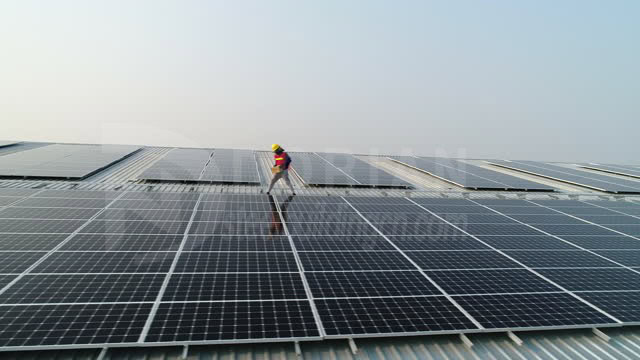
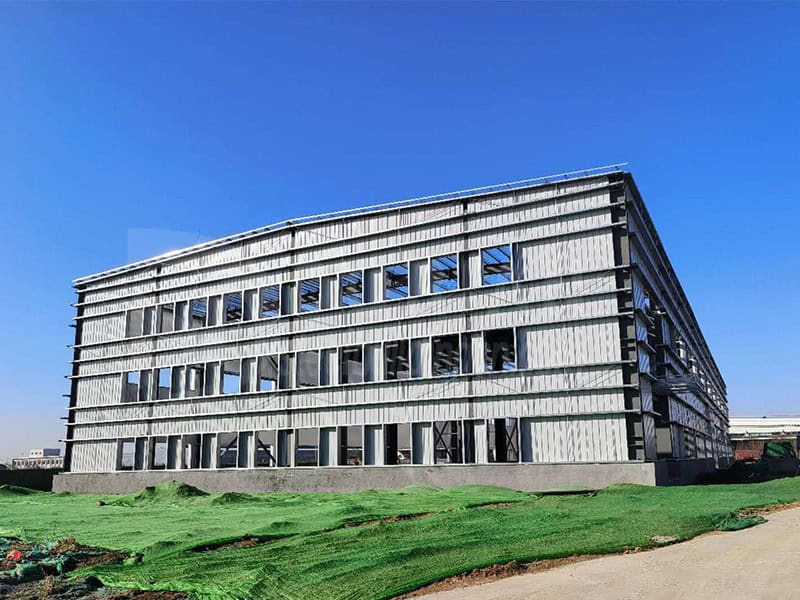
Background
In 2023, Dorian received an inquiry for a workshop from the client, whose initial request was rather simple: a strong and cost-effective building for a factory. Client claimed that he plan to build a tilapia fish farm, therefore, he need a factory for fish food to save the cost for fish farming, and also sell the products at local.
Designing
When Dorian contacted the client, he expressed that due to the local grid network's instability and frequent blackouts, so he decided to install a solar power system on the factory's roof. Additionally, the client wanted some offices and a monitoring room for the production line in the workshop, Dorian suggest that adding a mezzanine floor for offices and monitoring room can save the space. Responding to the client's demands, Dorian's engineers began crafting a proposal design.
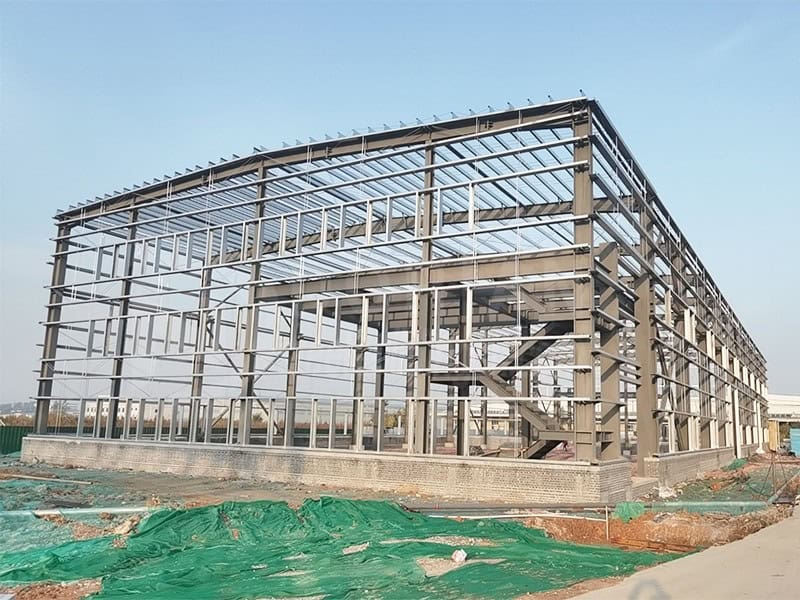
The day after receiving inquiry from the client, the proposal design was completed. As the solar panels on the roof would provide insulation for the building, reducing heat by approximately 40%, single steel sheet was chosen for the workshop's roof and walls to save costs. Inside, there would be a 50-square-meter, 3.5-meter-high mezzanine for offices, resting room and a monitoring room.
The client was satisfied by Dorian's efficiency and ability to provide solution that is compatable with his solar system project. It perfectly matched the client's requirements, and the offer fell within the client's budget, prompting him to sign the contract promptly.
Production&Delivery
The production of the steel structure only took two weeks: two days for designing all the parts of the structure, and eleven days for the production and packing. The entire project required four containers for shipping—three for the steel structure and one for the solar system.
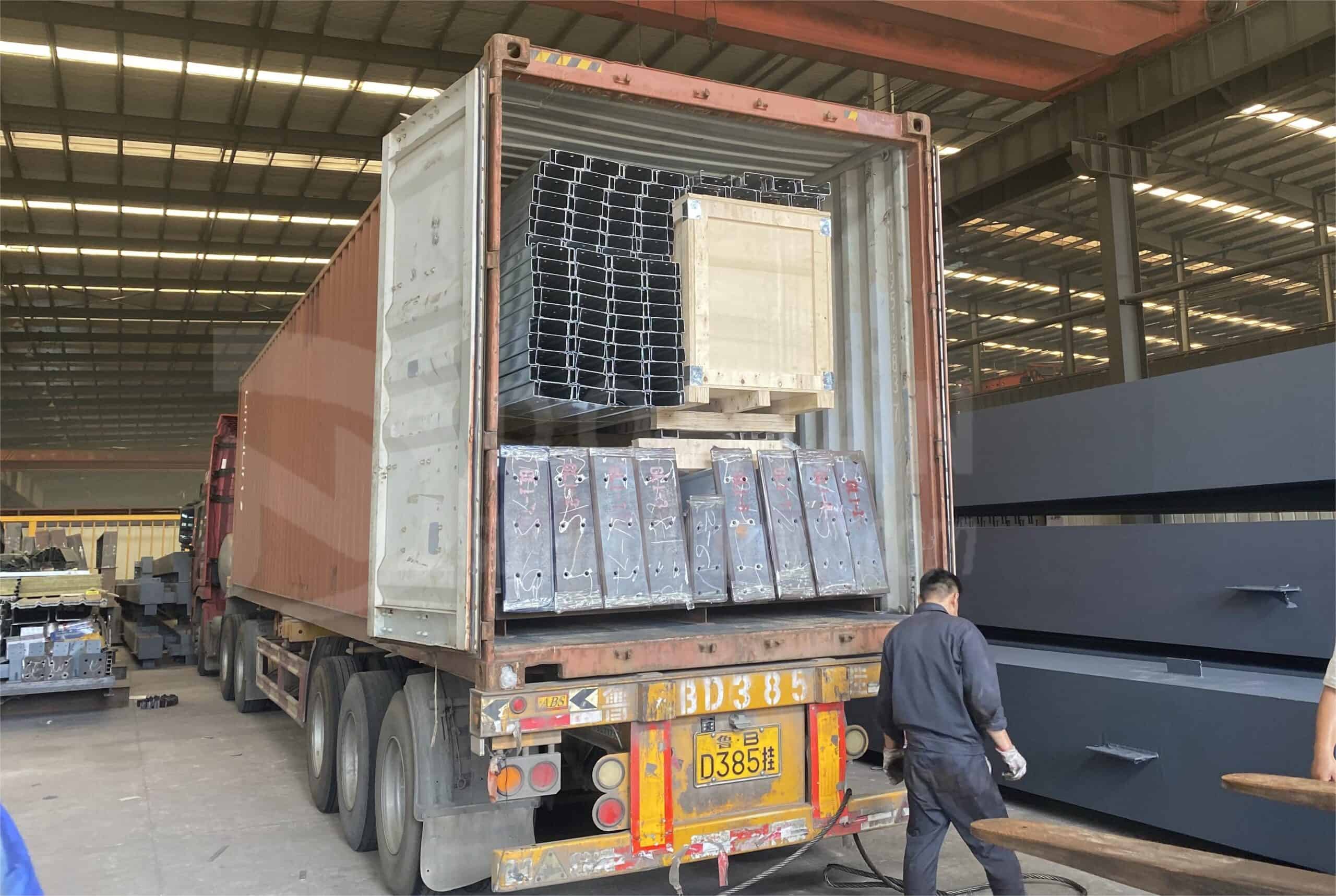
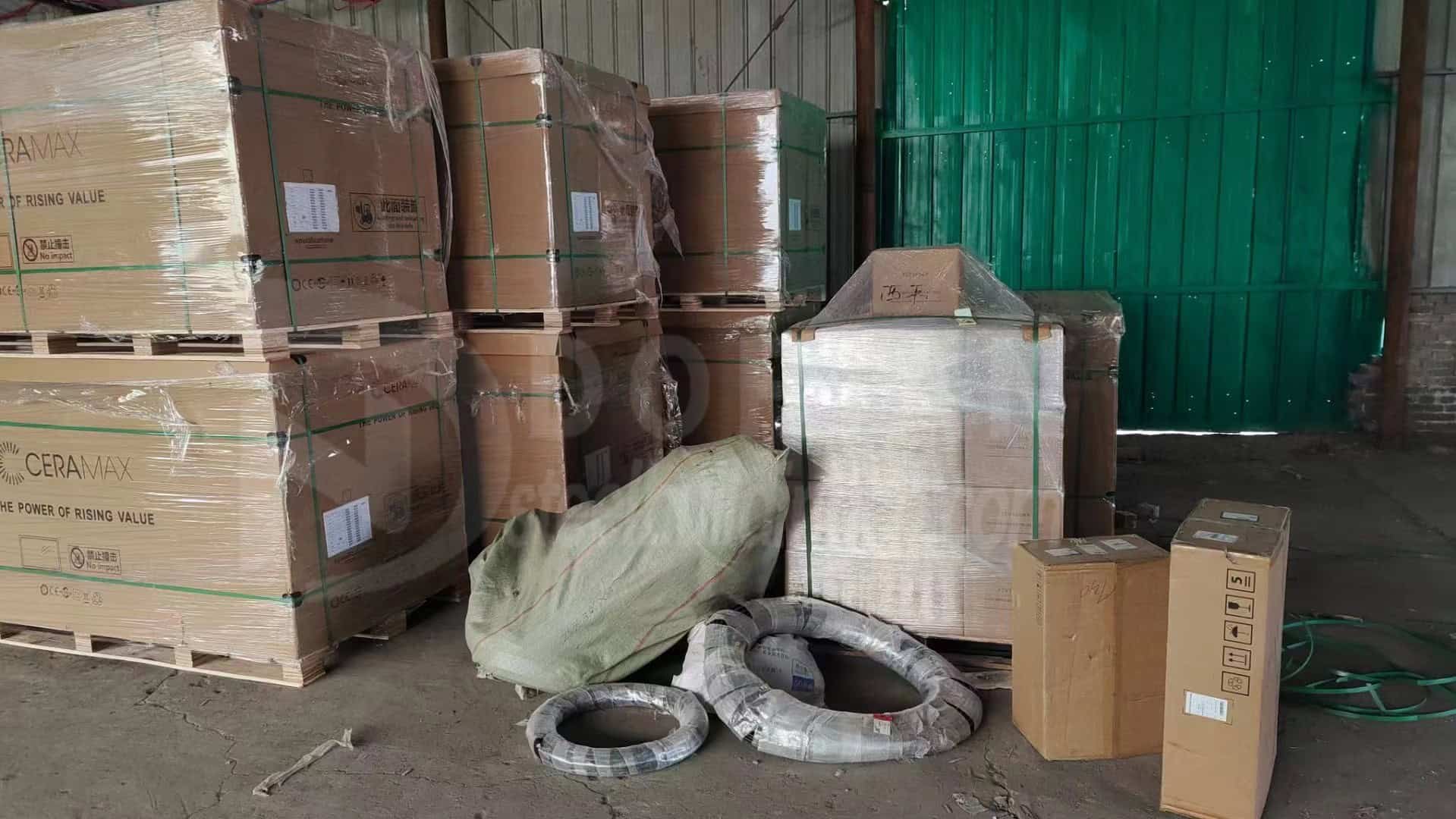
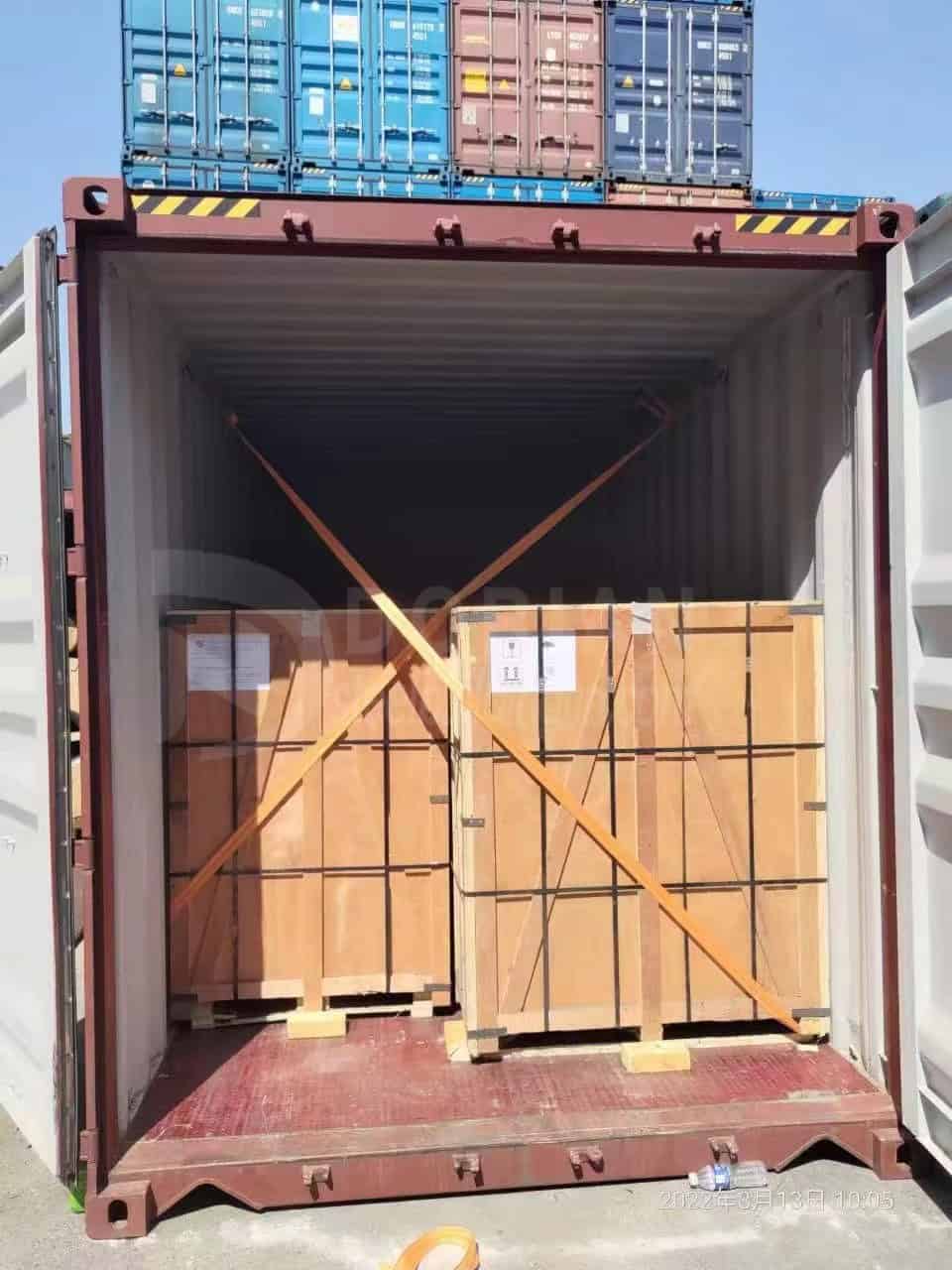
Installation:
The foundation plan was sent to the customer prior to shipment so that the foundation work has been completed before the customer receives the goods. Upon the cargo's arrival at the project site, the construction team finished the installation under Dorian's supervision and guidance. The erection process took only nearly one month. Then, Dorian’s electrical engineer provided guidance during the installation of the solar power system and ensured its connection to the grid.
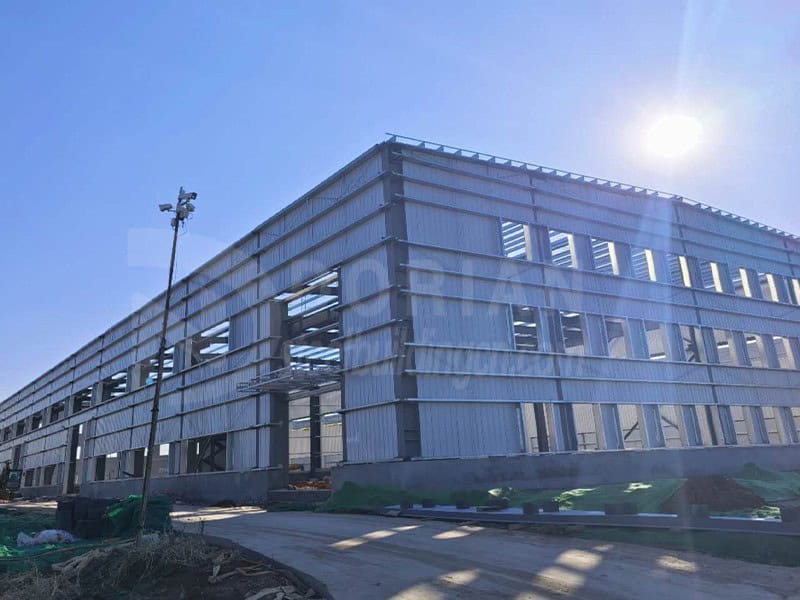
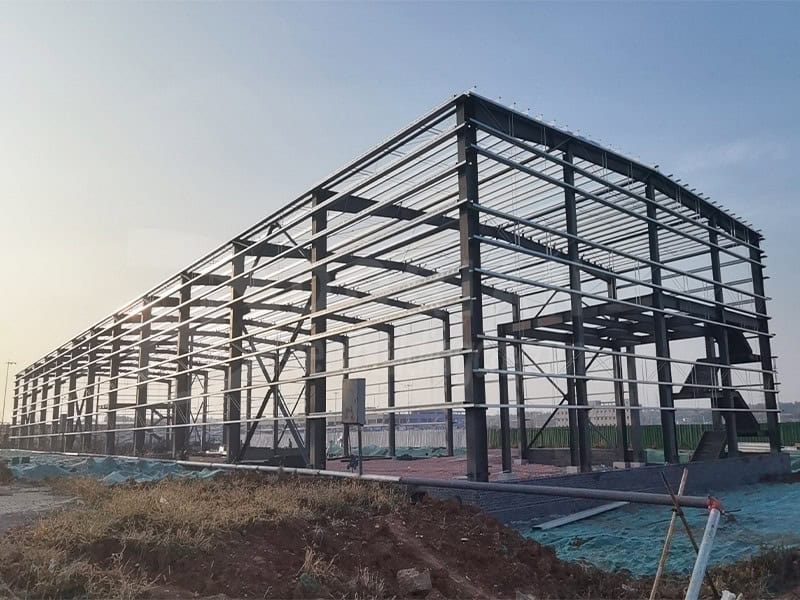