Project Name: Aluminum Alloy Window Production Plant
Dimensions: 15m (width) x 65m (length) x 10.15m (height)
Location: Bangkok, Thailand
Project Overview:
Dorian team is proud to present the steel structure warehouse solution designed for client’s aluminum alloy window production business in Thailand. The warehouse, measuring 15m (width) x 65m (length) x 10.15m (height), is tailored to meet production needs while combining functionality, durability, and aesthetic appeal.
Single-Slope Steel Frame with Parapet Walls:
The steel structure features a single-slope design, enhanced by parapet walls on all sides for a sleek and modern appearance.The steel beams and columns are painted in a vibrant orange-red color, adding a professional and visually appealing touch. Moreover,Louvers are installed around the walls to ensure proper ventilation, creating a comfortable working environment.
The roof and wall panels were designed with classic gray metal sheet, providing a cohesive and professional look.
A 3-ton overhead crane was also supplied by Dorian to facilitate the movement of window materials and streamline the production process.
Efficient Drainage System:
Gutters and downpipes are also installed along the eaves to ensure effective rainwater drainage, protecting the structure and maintaining a dry interior.
Convenient Access and Maintenance:
Two electric roller shutters are installed for easy access to the warehouse. A ladder is provided at the rear of the building, allowing workers to safely access the roof for inspection and maintenance.
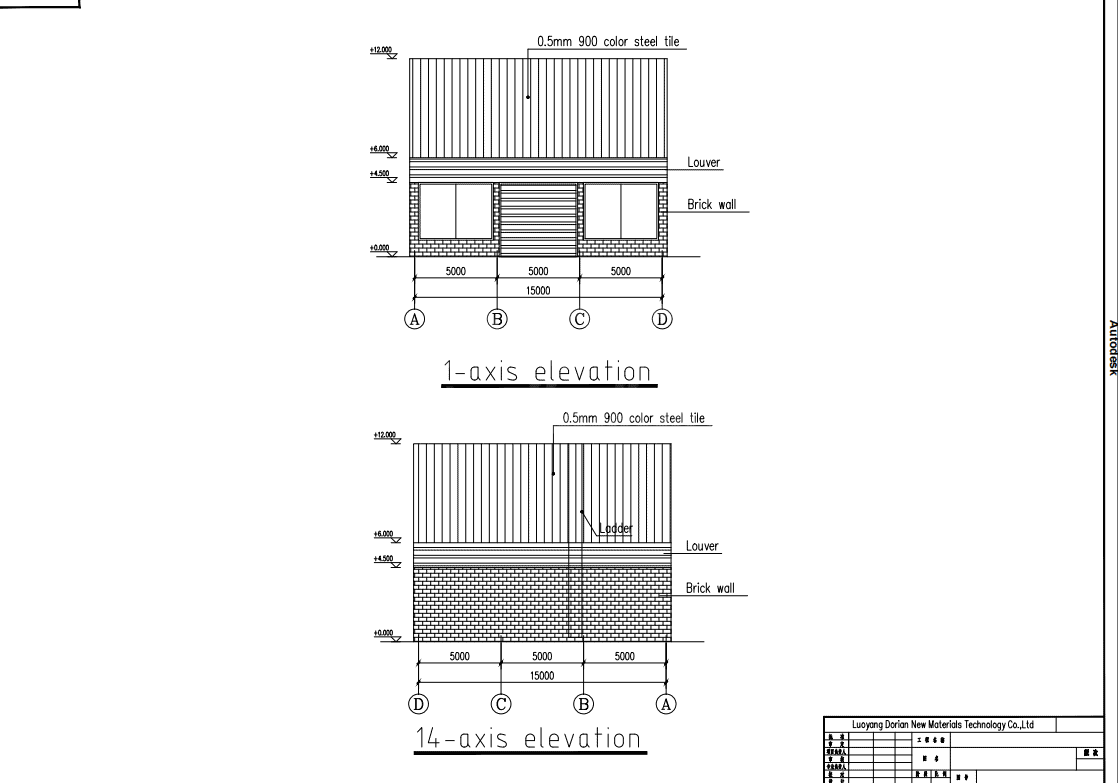
Production:
During the production phase, the client visited Dorian factory and were highly impressed by production scale, manufacturing capabilities, and product quality. To make the client’s trip more memorable, Dorian team arranged visits to Luoyang’s famous tourist attractions, including the White Horse Temple and Shaolin Temple. These experiences left a lasting impression and further strengthened our partnership.
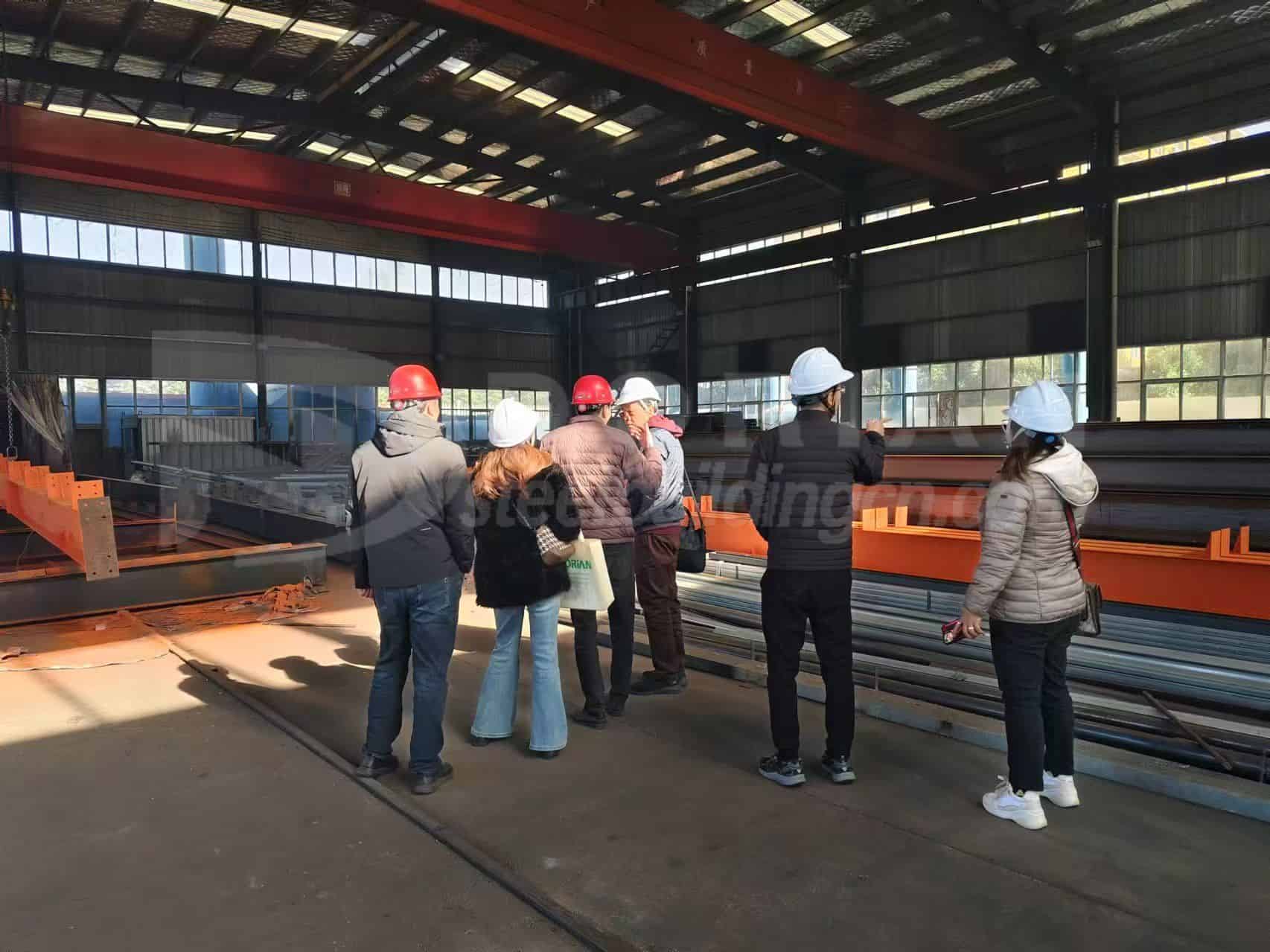
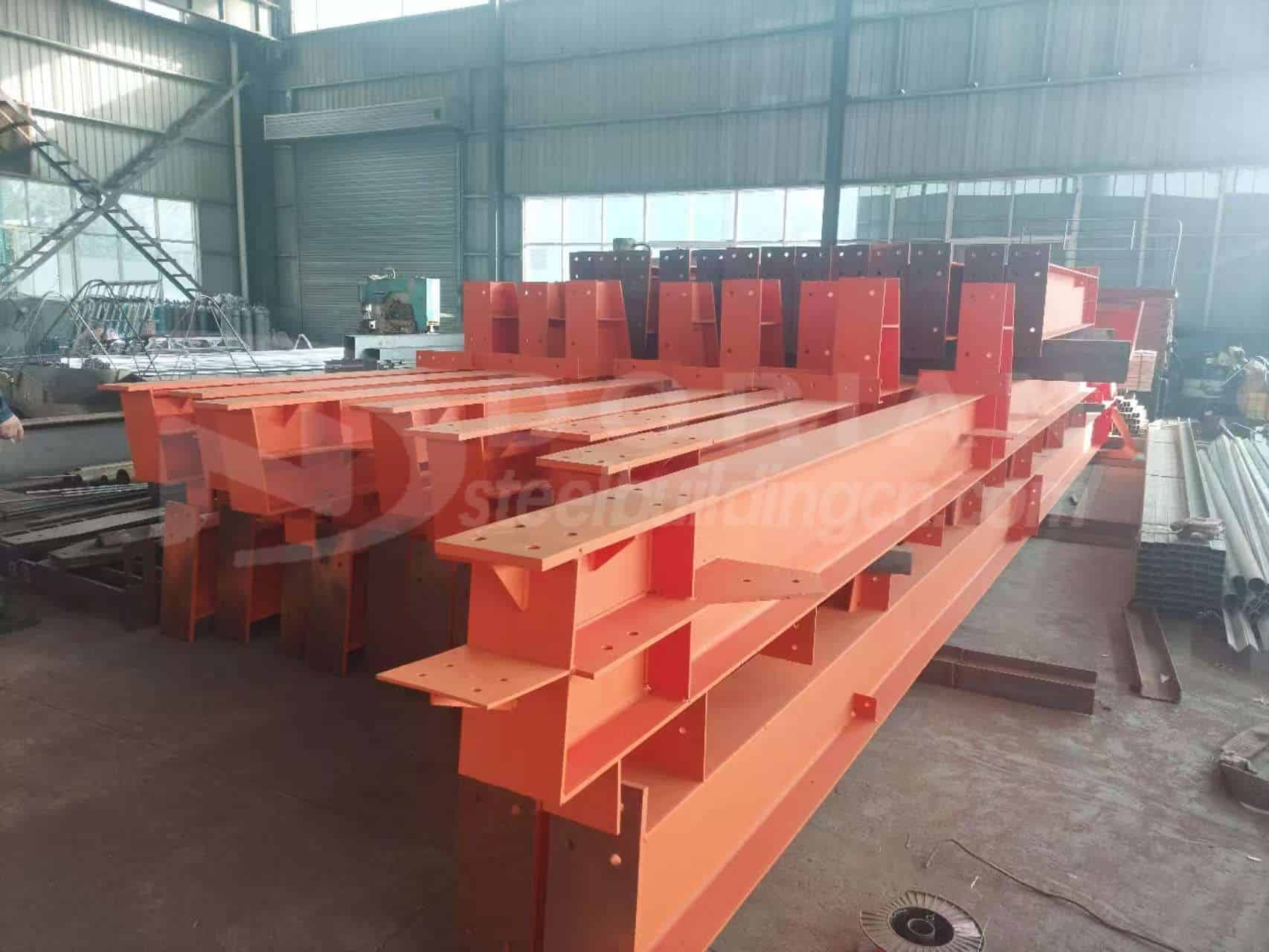
Delivery and installation: The materials were finished in approximately 25 days and took about 10 days delivered to the project site.Dorian’s professional installation team was dispatched to complete the installation work for client. As of now, the entire steel structure installation has been successfully completed.
Only the brick wall construction remains, which is being handled by local workers. The warehouse is expected to be operational within this month.
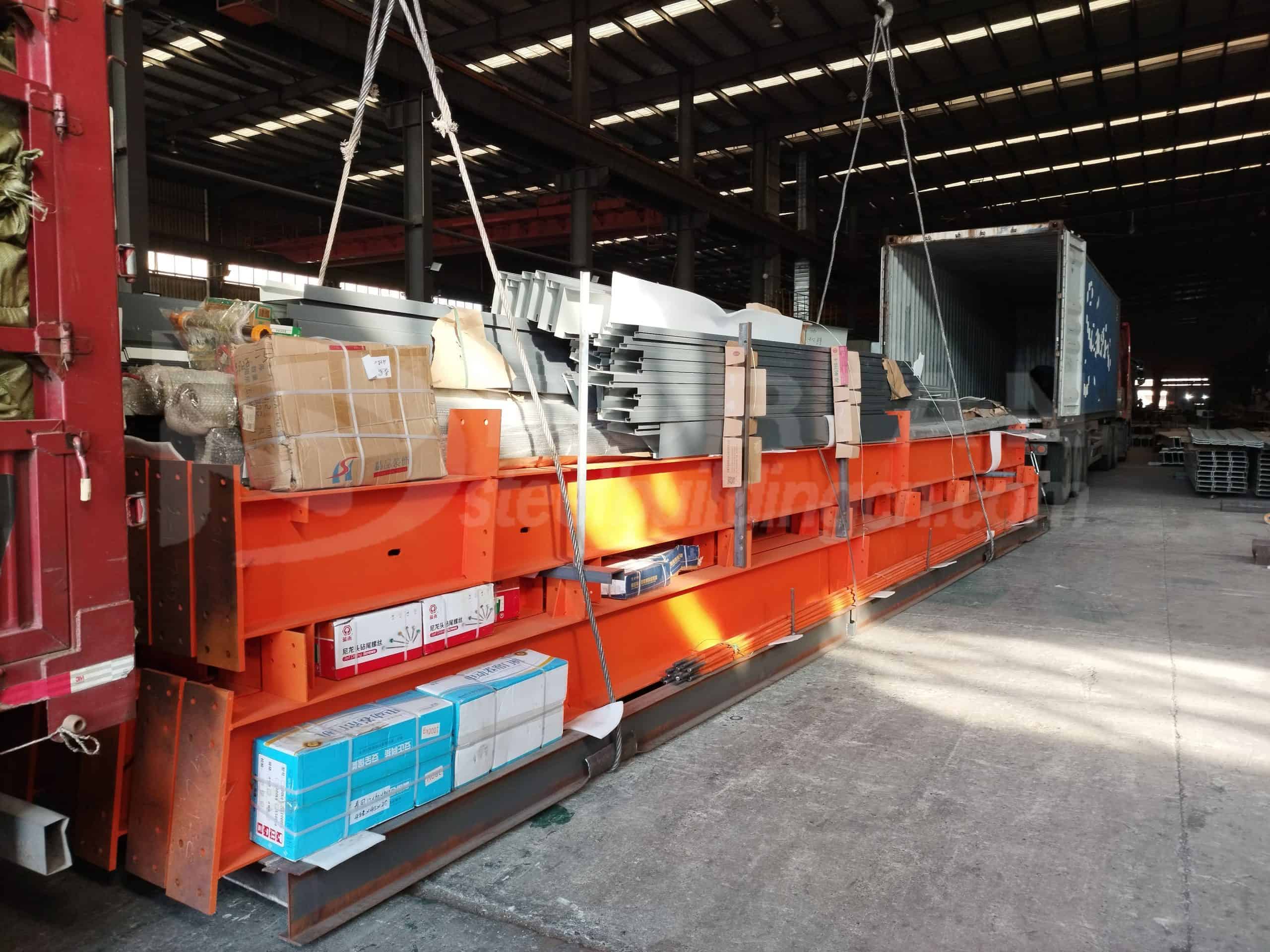
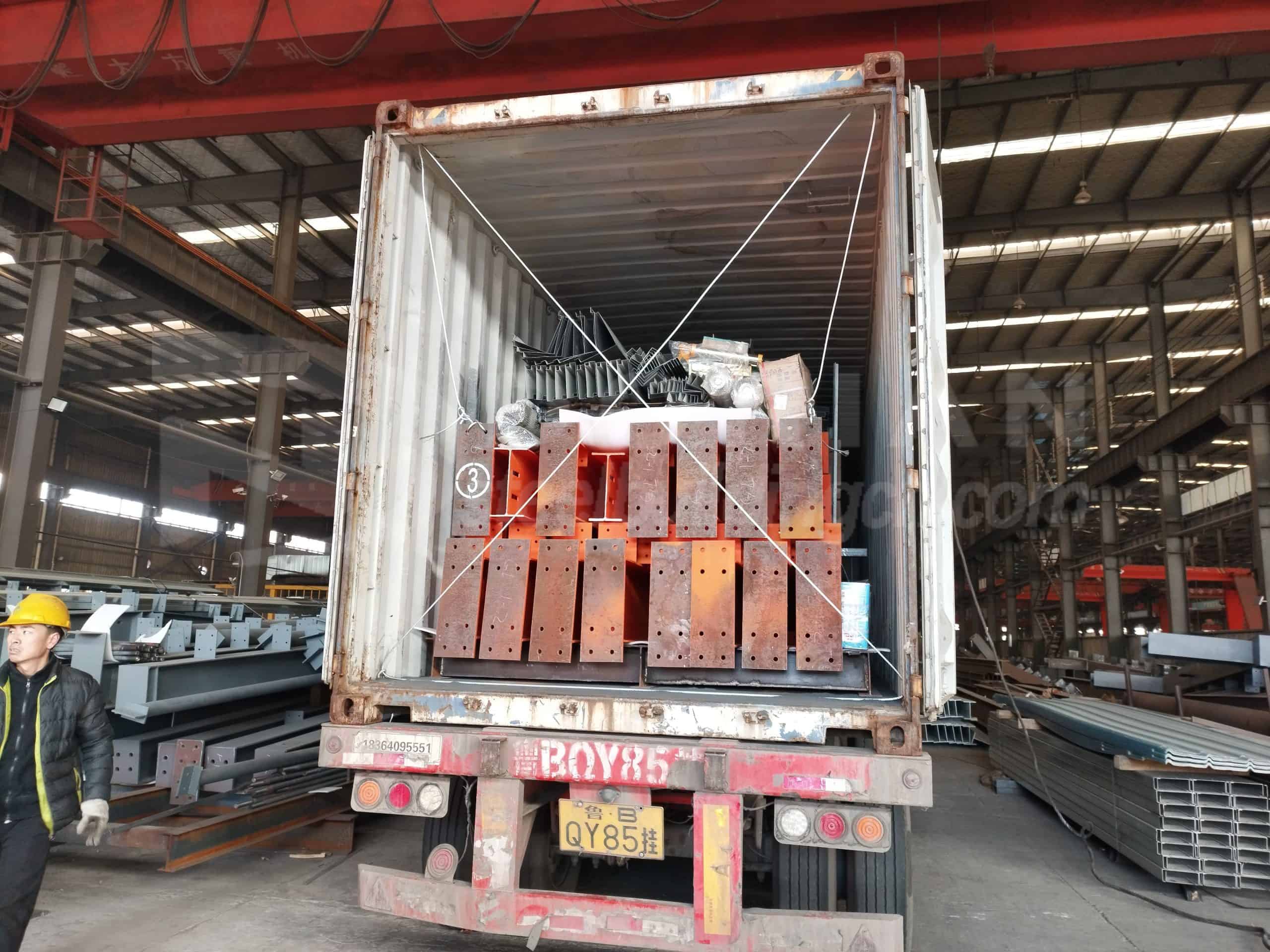
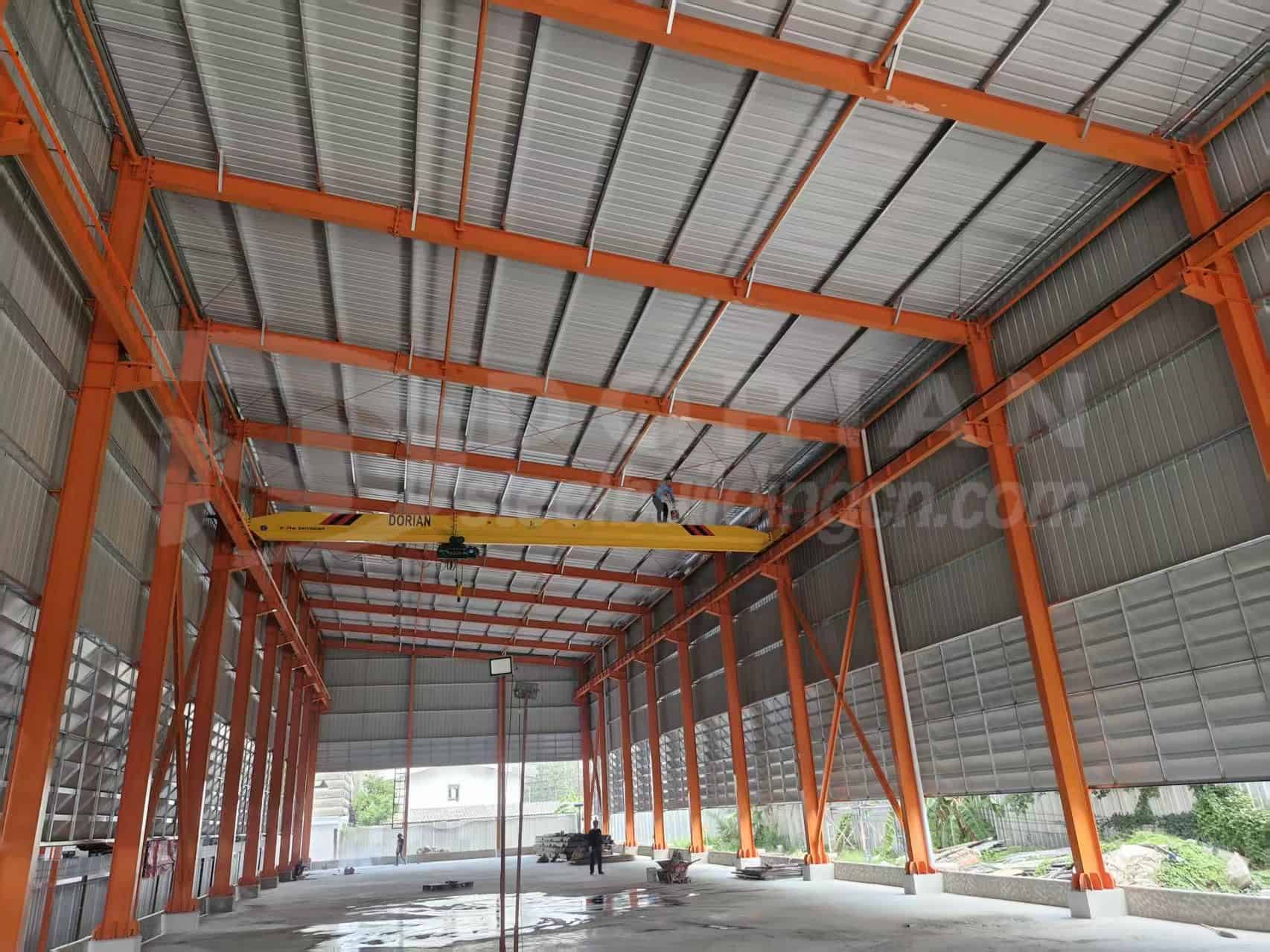
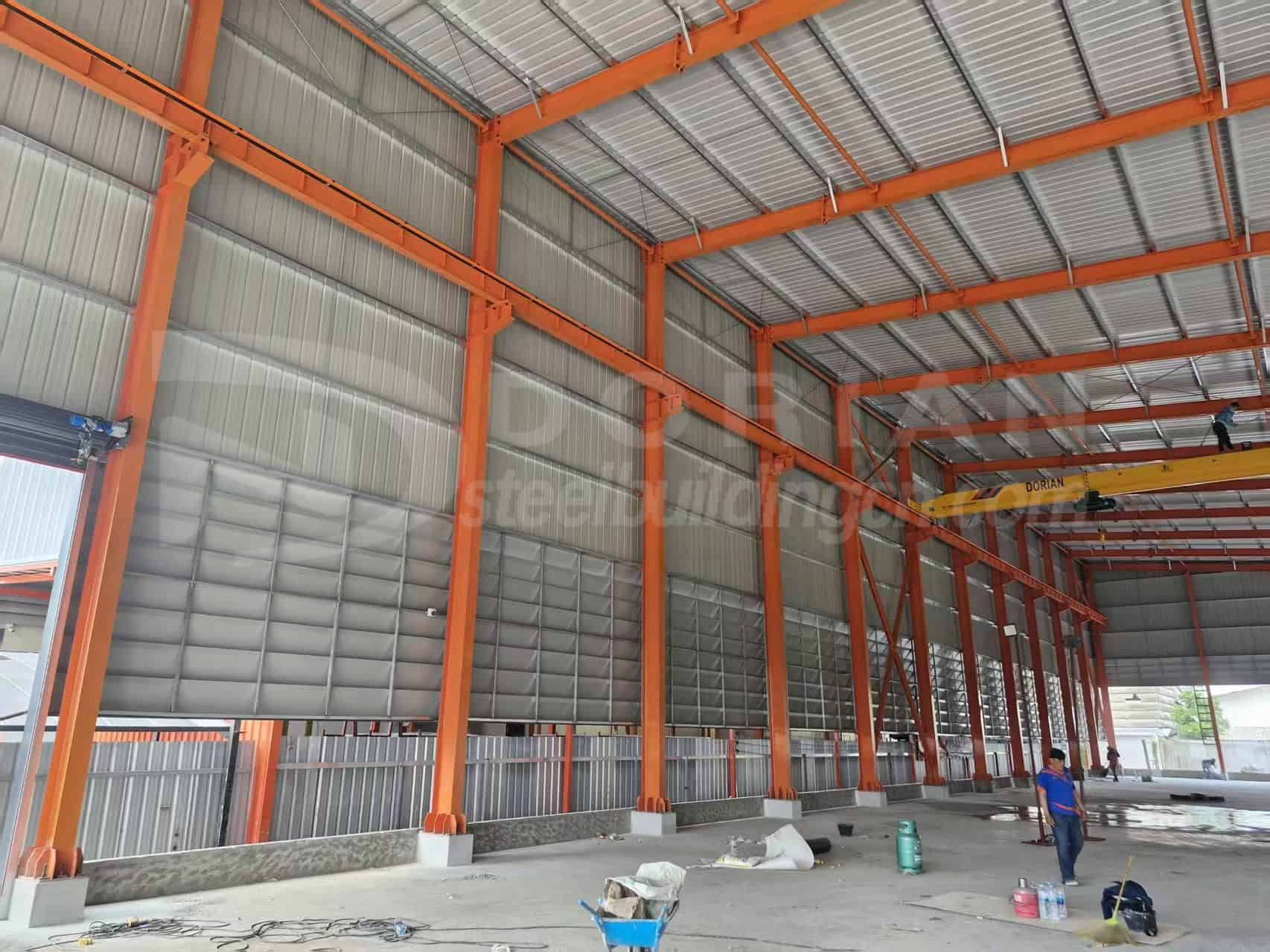
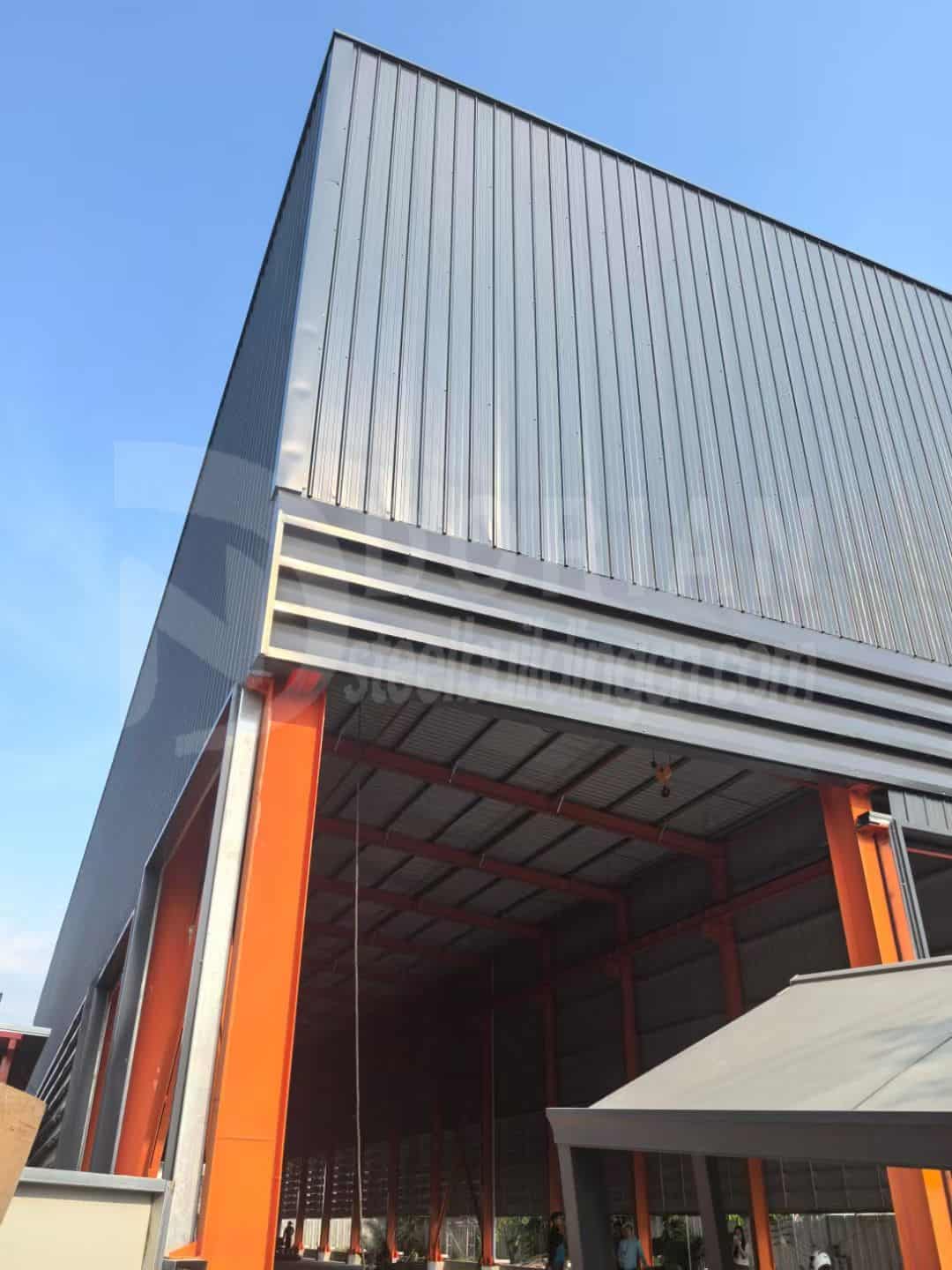
Ongoing Collaboration:
New Energy System:
Dorian team and client is currently discussing a new energy solution for the finished 15*65*10.15m project.. The plan includes installing solar panels on the roof and providing a comprehensive system to enhance energy efficiency. The new energy technician is also being fine-tuned with client in Thailand and working on the final details.
5-Story Commercial Building Project:
The preliminary drawings and a quotation of 5-story commercial building project have been provided for client . The details are under further discussion and collaboration continues to grow.
Please do not hesitate to contact us If you need a steel structure project. Dorian engineer will customize the solution according to your project details.
Looking forward to continuing our successful partnership and supporting your business growth in Thailand and beyond.